Кайзены побеждают санкции и кадровый голод
Как Горьковский автозавод наращивает производительность труда в условиях турбулентности и нехватки персонала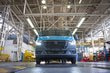
Напряженность на российском рынке труда растет: Банк России отмечает острый дефицит кадров в промышленном секторе и ожидает снижения уровня безработицы по итогам 2024 г. до исторических 2,6% (3,2% в 2023 г.). Из-за нехватки людей компании отказывались от части заказов, переносили сроки реализации инвестпроектов и повышали зарплаты, отмечает ЦБ в июльском докладе о состоянии региональной экономики.
Дефицит кадров надолго останется главным фактором, сдерживающим развитие промышленности в России. Сейчас экономике не хватает примерно 1,6 млн человек, а к 2030 г. дефицит может увеличиться до двух – 4 млн человек, указывал руководитель направления инноваций hh.ru Никита Бугров в презентации «Стратегический взгляд на рынок труда». Минтруд оценивает дополнительную потребность российской экономики в кадрах к 2030 г. в 2,4 млн человек, рассказывал министр труда и социальной защиты РФ Антон Котяков в интервью «Интерфаксу» в июне.
Дефицит трудовых ресурсов в России – при всех негативных последствиях, вроде разгона уровня зарплат и замедления роста производства, – дает экономике мощный стимул для трансформации, следует из доклада ЦБ. Чтобы справиться с нехваткой рабочих рук, предприятия инвестируют в автоматизацию производства, установку роботов и совершенствование внутренних процессов.
Повышение производительности труда – главный инструмент борьбы с кадровым голодом, отмечало Минэкономразвития России в прогнозе на 2024‒2026 г. Министерство ожидает рост производительности на 1,6% в 2024 и 2025 г. и на 1,9% в 2026 г. Для сравнения, производительность труда в странах ОЭСР (38 государств, большинство – члены Евросоюза) в период с 2011 по 2020 г. росла в среднем на 1,1% в год, а затем и вовсе снизилась в 2021 и 2022 гг., говорится в отчете PWC «Барометр рынка труда 2024».
В российской промышленности есть наглядные примеры того, как совершенствование внутренних процессов и повышение производительности труда помогают справляться с нехваткой кадров, падением спроса, санкциями и сбоями в цепочках поставок. Академический руководитель магистерской программы «Операционная эффективность и производственные системы» Высшей школы бизнеса НИУ ВШЭ (ВШБ) Григорий Баев в сборнике «Операционная эффективность» серии «Новое в менеджменте» называет Горьковский автозавод именно таким примером антикризисного менеджмента в автопроме.
Кейс предприятия и его производственную модель студенты ВШБ разбирают как модель лучших практик, которую можно масштабировать и применять в других российских компаниях. Производитель «Газелей», «Соболей» и «Газонов» первым в России по инициативе промышленника Олега Дерипаски внедрил производственную систему 20 лет назад и благодаря этому многократно увеличил производительность труда, несмотря на кризисы, ни разу не остановил производство и из убыточного предприятия превратился в одного из лидеров отечественного автопрома.
Искусство непрерывных изменений
«Производственная система ГАЗ – это не только набор инструментов управления производственными процессами, а философия бережливого производства и постоянного улучшения, которая охватывает всех сотрудников», – объясняет директор по производственной системе предприятия Оксана Исакова. Эта система, по ее словам, построена по принципам Toyota Production System. В ее основе – измерение и стандартизация всех процессов и их непрерывное совершенствование, в которое вовлечен весь персонал. Каждый сотрудник может предложить, как сделать его участок работы более экономичным, быстрым и эффективным, а компания оперативно внедряет такие предложения (кайзены).
Внедрять новую производственную систему Горьковский автозавод начал не от хорошей жизни. К началу 2000-х предприятие находилось в состоянии глубокого кризиса, вспоминает Исакова. У завода был огромный запас нераспроданных машин, большие долги перед банками и поставщиками, хронические простои сборочных конвейеров и значительная доля брака. В тот период на предприятие пришла новая команда во главе с Олегом Дерипаской, который, побывав на заводах Toyota, решил внедрить на заводе в Нижнем Новгороде подход японского автохолдинга к умной организации труда.
Пилотным участком в 2003 г. стал цех по сборке кабин «Газелей». Проектная команда во главе с Дерипаской с хронометром изучила все производственные процессы. Выяснилось, что операторы конвейера тратят много времени на лишние переходы, подолгу ждут нужные комплектующие, спотыкаются о запасы деталей. Вместе с консультантами Toyota завод разработал новые эргономичные рабочие места, изменил схему подачи комплектующих и деталей.
Результаты превзошли все ожидания. По данным, приводимым в сборнике «Операционная эффективность», за первый год без особых затрат производительность участка выросла в четыре раза (на предприятии производительность рассчитывается как сравнение отработанных часов к плановому показателю). Численность работников цеха за это же время уменьшилась с 258 до 196 человек, а количество собираемых за смену кабин увеличилось с 98 до 146.
Важным результатом стало создание удобных рабочих мест. Один из примеров, по словам Исаковой, – изменение операций по установке лобового стекла. Раньше операторам приходилось подниматься по несколько десятков раз в день с пола на конвейерную ленту с 20-килограммовым стеклом в руках. Завод установил подиумы, чтобы лента конвейера и пол находились на одном уровне. «Когда людям стало проще работать, они стали позитивно смотреть на изменения и более активно в них участвовать», – вспоминает Исакова.
Вслед за пилотным участком начали меняться другие цеха и процессы на Горьковском автозаводе, причем не только на производстве, но и в логистике, управлении персоналом и цепочками поставок. Стандартизация позволила организовать производство по принципу «точно в срок», когда каждое звено цепочки процесса синхронизировано с другими. Автозавод перешел от производства впрок к выполнению заказов потребителей на определенные модификации грузовиков.
«В первые годы внедрения производственной системы мы повышали производительность на 20-30% в год, и это давалось очень легко. Сейчас, когда основные процессы отлажены, мы продолжаем постоянно внедрять кайзены и улучшения и держим планку в 5% ежегодного прироста производительности труда», – говорит директор по производственной системе. В 2023 г., по ее словам, это дало дополнительный экономический эффект в 381 млн руб. Финансовые и операционные результаты работы компания не раскрывает с 2018 г. По данным Росстата, в первом полугодии 2024 г. в России выпущено 90 000 грузовиков – на 21% больше, чем в первом полугодии 2023 г. Производство легковых машин за то же время выросло на 62%.
Изменениям нужен человек
Постепенно новые подход и философия охватили все подразделения нижегородского автозавода. И у сотрудников появилась заинтересованность в том, чтобы самим предлагать новые решения для оптимизации любых процессов. Каждый год работники автозавода подают около 9000 предложений-кайзенов, и примерно 95% из них реализуются.
В 2008 г. на базе корпоративного учебного центра – кампуса с 30 аудиториями, лабораториями и 400 программами обучения разного профиля – возникла новая система обучения персонала по компетенции «Бережливое производство». Она предназначена для подготовки и переподготовки сотрудников автозавода, поставщиков и представителей других компаний, заинтересованных во внедрении собственной производственной системы, рассказывает директор Академии современных технологий автомобилестроения им. А. Н. Моисеева Галина Бирюкова. По ее словам, обучение производственной системе на продвинутом уровне проходят сотрудники всех руководящих позиций предприятия. Они знакомятся с философией производственной системы не только в классах, но и на практике, с хронометром, учатся выявлять проблемы на конвейере и решать их.
Линейный персонал также в обязательном порядке знакомится с производственной системой ГАЗа в корпоративном университете в рамках профессиональной подготовки, но основное обучение происходит на рабочем месте под руководством опытных специалистов. «В прошлом году мы запустили новую программу наставничества, и теперь все наставники проходят подготовку: мы учим их правильно объяснять новичкам особенности операций, корректно давать обратную связь, работать со взрослыми людьми», – уточняет Бирюкова.
После того, как завод внедрил производственную систему у себя, он вплотную занялся ее распространением у поставщиков и партнеров.
«Как потребитель мы покупаем у поставщиков не просто детали, а весь процесс: нам важно, чтобы он обеспечивал качество и своевременные поставки нужных объемов, – объясняет Исакова. – Поэтому, когда мы выбираем нового поставщика, мы обязательно приглашаем его на наш завод изучить производственную систему, помогаем провести аудит его производства и внедрить лучшие практики, обучаем сотрудников партнера.» Благодаря стратегическому видению Олега Дерипаски, который еще 20 лет назад внедрил на предприятии производственную систему, она получила распространение и во всей отрасли, отмечает Исакова.
В качестве примера она приводит производителя бортовой фурнитуры для грузовиков. В 2015 г. с деталями от этого поставщика постоянно случались сбои и проблемы. Сотрудники ГАЗа изучили подробно, как выстроены процессы партнера, помогли оптимизировать процессы на участке механообработки картера, устранить неоптимальные процессы, поднять производительность и высвободить лишние площади. В результате сокращения себестоимости производитель автокомпонентов сумел поднять зарплату своим сотрудникам, устранив текучку кадров, и снизил цены на продукцию на 2%. Производственная система ГАЗ сейчас охватывает всех ключевых поставщиков предприятия и 60-70% второстепенных (их сотрудники проходили обучение на нижегородском автозаводе), всего у компании около 3000 поставщиков, говорится в сборнике ВШБ «Операционная эффективность».
Принципы производственной системы применимы везде, поэтому в учебный центр предприятия приезжают специалисты из банковской сферы, сферы страховых услуг, сельского хозяйства и т. д., рассказывает Бирюкова. По ее словам, учебную программу нижегородского автозавода отличает практическая направленность: 80% обучения проходит на производственной площадке и в цехах.
Например, на нижегородском автозаводе изучали производственную систему три команды из компании «Информационные спутниковые системы им. академика М. Ф. Решетнева»: лидеры по направлениям, начальники цехов, а также технологи и мастера. «Важно, что обучение проводится на производстве: ты сам делаешь хронометраж, ищешь потери, внедряешь кайзен и видишь, что изменилось», ‒ говорит начальник службы по развитию производственной системы компании Анатолий Абраменков. По его словам, такое обучение позволило убедиться на практике, что улучшения – это постоянный процесс, который меняет условия труда и помогает найти новые решения для сокращения потерь. Внедрив принципы бережливого производства в цехах, компания стала улучшать процессы у конструкторов. Также здесь решили поощрять не только тех, кто предлагает кайзен, но и всю команду, участвующую в его внедрении.
Роботы, автопилоты и технологии будущего
Главная проблема в отрасли сейчас – нехватка кадров, признают на нижегородском автозаводе. Стандартных инструментов производственной системы – поиска и устранения потерь – уже недостаточно, чтобы компенсировать нехватку рабочей силы. «Поэтому главным направлением повышения производительности теперь становится автоматизация, – рассказывает директор по производственной системе Горьковского автозавода. – У нас на предприятии роботизированное сварочное и штамповочное производство, высокотехнологичный окрасочный комплекс, но теперь мы начинаем внедрение роботов повсеместно там, где раньше использовался ручной труд».
Например, одно из направлений развития производственной системы предприятия – внедрение беспилотного транспорта. «На наших конвейерах большое количество деталей, четкая ритмичность процессов, для которой требуется своевременная подача комплектующих со склада. С этой задачей может хорошо справиться беспилотный транспорт и заменить часть водителей погрузчиков», – объясняет Исакова.
В 2023 г. предприятие закупило и настроило партию беспилотных транспортных платформ для подачи комплектующих, а в этом году начало делать их самостоятельно. Пока на Нижегородском заводе действуют девять маршрутов, по которым на конвейер доставляется 140 компонентов, но до конца года автопроизводитель надеется запустить 34 маршрута для доставки более 500 деталей.
Параллельно при поддержке Российского фонда развития информационных технологий Горьковский автозавод разворачивает систему мониторинга промышленного оборудования. Эта программа позволяет управлять производством на основе данных в режиме реального времени: оценивает свободные мощности и эффективно перераспределяет загрузку оборудования. К «Диспетчеру» будет подключено 190 единиц оборудования: обрабатывающие центры, робототехнические комплексы, конвейеры, лазеры, токарные и фрезерные станки. Интегратор проекта ГК «Цифра» ожидает, что использование решения позволит увеличить эффективную загрузку подключенного оборудования на 15%, говорилось в совместном сообщении автозавода и «Цифры».