Промышленность ставит на цифру
Как крупнейшие российские предприятия используют расширенную автоматизацию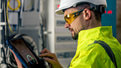
Пионеры цифровизации во всем мире – финансовый сектор и телеком, а промышленность, как правило, более консервативна. В России же проекты по расширенной автоматизации наиболее активно внедряют компании ресурсной сферы: нефтяники и металлурги. И представители этих предприятий уже говорят об экономическом эффекте в десятки миллиардов рублей. Сейчас проекты по цифровизации также запускают в сельском хозяйстве, химической и атомной промышленности.
В 2021 г. отечественные предприятия из добывающей, обрабатывающей, сельскохозяйственной промышленности и ТЭКа потратили на покупку, создание, распространение и использование цифровых технологий и связанных с ними продуктов и услуг 478,9 млрд руб. По оценке АНО «Цифровая экономика», в 2022 г. промышленность вложила в цифровизацию не меньше. При этом объем рынка искусственного интеллекта (ИИ) в России в 2021 г. составил около 550 млрд руб. И рентабельность компаний, внедряющих такие технологии, выросла в среднем на 5%. Аналитики Центра компетенций ИИ Сбербанка отметили, что внедрение технологий ИИ может сыграть ключевую роль в росте ВВП страны на 1% уже к 2025 г.
Но как показало исследование компании Technored, проведенное летом 2023 г., 47,4% представителей компаний промышленного сектора оценили уровень автоматизации и внедрения робототехники на своих предприятиях как низкий. Только 15,8% участников опроса заявили, что в их компаниях высокий уровень автоматизации.
Цифровые баррели
Лидеры по внедрению технологий расширенной автоматизации – компании добывающей промышленности, обладающие достаточным количеством свободных средств и получающие от инноваций более осязаемую выгоду за счет больших оборотов. Так, «Роснефть» в 2019 г. запустила технологию цифровых двойников на Илишевским месторождением «Башнефти». Информационная система в реальном времени удаленно отслеживает все параметры работы месторождения. 3D-визуализация позволяет учитывать специфику производства и ландшафт местности. Сейчас у компании уже более 50 000 цифровых двойников скважин и производственных объектов. Осенью 2022 г. в «Роснефти» сообщили, что начали использовать решение на базе нейросетей, которое позволяет подобрать оптимальные варианты разработки каждого участка месторождения. По оценке самой компании, технология позволит увеличить прибыль от разработки месторождения до 30%.
Компания «Газпром нефть» по итогам 2020 г. сообщила, что получила экономический эффект в 7,2 млрд руб. в результате внедрения цифровых инструментов. Компания запустила более 150 новых цифровых инициатив и 10 программ цифровой трансформации. В марте 2023 г. «Газпром нефть» сообщила о создании цифрового двойника месторождения им. Александра Жагрина в Кондинском районе ХМАО – Югры. Согласно прогнозам компании, экономический эффект от этого проекта может составить более 1 млрд руб. до конца 2023 г. Также в этом году «Газпром нефть» внедрила цифровую платформу для взаимодействия заказчиков и исполнителей нефтесервисных услуг. Сейчас к ней подключено более 250 контрагентов, они могут в один клик оформить пропуск на месторождение, заказать топливо и материально-технические ресурсы, арендовать технику, составить и проконтролировать график работ.
«Татнефть» внедрила технологию цифровых двойников на Ромашкинском и Ново-Елховском месторождениях, а также на Альметьевской и Абдрахмановской площадях. По подсчетам компании, технологией охвачены активы, отвечающие за 80% добычи нефти.
Помощник металлурга
Металлургический сектор не сильно отстает от нефтегаза по использованию инструментов цифровизации. Например, НЛМК инвестирует в автоматизацию производства около $50 млн в год. Цех горячего проката оборудовали системой автоматического распределения слябов по нагревательным печам и регулирования паузы между слябами при выдаче в прокат. Также в цехе запустили автоматический контроль качества смотки при помощи лазерного сканера. Другой проект НЛМК – автоматизированная система отслеживания состояния тележек обжиговой машины, использующая системы компьютерного зрения, которая экономит компании около 41 млн руб. в год. Всего команда комбината реализует более 200 проектов автоматизации производства. По подсчетам компании, использование data science (наука о данных) и машинного обучения для оптимизации параметров коксохимического производства принесло совокупный экономический эффект в 1,4 млрд руб.
Магнитогорский металлургический комбинат (ММК) осенью 2023 г. запустил систему безопасности для персонала на основе беспроводной передачи данных малого радиуса действия (NFC). На одежде сотрудников закрепили датчики, а приемники сигнала расположили на опасном оборудовании. Когда люди подходили слишком близко к такой технике, радиометки на экипировке работников начинали вибрировать. На оборудовании в это же время блокировались механизмы и включалась световая и звуковая сигнализация.
Другой проект ММК – система аналитики качества продукции на базе машинного обучения и ИИ. Она контролирует продувку металла аргоном. Комплекс, установленный на агрегате печь-ковш, состоит из роботизированного манипулятора и камеры в защитном кожухе, позволяющем вести видеозапись при высоких температурах. Полученные кадры обрабатывают сразу несколько математических моделей на основе нейронных сетей, выдающих рекомендации по оптимальному режиму работы для металлургов.
«Северсталь» с 2016 г. внедряет проект по автоматизированному контролю качества продукции с использованием технологий компьютерного зрения. Система определяет брак по малозаметным визуальным признакам, анализируя видео с десятков камер. С помощью этого решения компания контролирует выпуск 4,2 млн т продукции при общем объеме производства около 10,7 млн т. В «Северстали» сообщали о снижении среднего уровня претензий к качеству в цехе на 55%. Компания уже инвестировала в проект 1,28 млрд руб., в планах – вложить не менее 2 млрд руб. При этом, однажды обучив систему, ее можно довольно быстро перенастроить под параметры схожего производства, так что в «Северстали» не исключают, что смогут масштабировать решение на партнерские предприятия.
ИИ-агроном и компания
В «Росатоме» уже шесть лет занимаются программной роботизацией, чтобы снять с сотрудников рутинные монотонные задачи. В начале компания использовала зарубежные решения, а в 2020 г. приступила к разработке собственного. В конце 2021 г. госкорпорация запустила в эксплуатацию RPA-платформу «Атом.РИТА» (роботизированный интеллектуальный технологичный ассистент). В итоге свыше 400 роботов осуществляет более 10 млн операций в год и освобождает от рутины более 240 человек, рассказал представитель «Росатома».
Решения расширенной автоматизации начинают использовать и в других отраслях промышленности. Например, технологии машинного обучения помогли холдингу «Русагро» решить задачу оптимального расположения кагатов свеклы. Кагаты – насыпь из уже собранных корнеплодов прямо на поле, где урожай временно хранится. От особенностей участка зависит в том числе сахаристость свеклы. Специалисты компании собрали с нескольких полей данные о расположении горок урожая, температуре, качествах корнеплодов. Этот массив информации пропустили через систему аналитики и получили модель, позволяющую выбирать оптимальное место на поле для хранения свеклы и определять очередность отправки партий продукции на завод. Реализация проекта заняла три месяца, а эффект от него составил сотни миллионов рублей, оценили в компании.
Еще одна разработка «Русагро» – нейросеть для идентификации различных сорняков и вредителей на полях по снимкам с дронов. Сейчас в базе системы более 150 сорных растений.